化工工艺流程设计基础知识,果断收藏了!
工艺流程设计是工艺设计的核心!
工艺流程设计的成品通过图解形式(形象、具体)地表示——工艺流程图,它反映了化工生产由原料到产品的全部过程既物料和能量的变化,物料的流向以及生产中所经历的工艺过程和使用的设备仪表。
工艺流程图集中地概括了整个生产过程的全貌。生产同一化工产品可以采用不同原料,经过不同生产路线而制得,即使采用同一原料,也可采用不同生产路线,同一生产路线中也可以采用不同的工艺流程。
选择生产路线也就是选择生产方法,这是决定设计质量的关键。如果某产品只有一种生产方法,就无须选择;若有几种不同的生产方法,就应逐个进行分析研究,通过各方面比较筛选一个最好的生产方法,作为下一步工艺流程设计的依据。
可靠性:
流程是否通畅、生产是否安全、工艺是否稳定、消耗定额、生产能力、产品质量和三废排放是否达到预定指标。
适用性:
和具体环境、资源和技术的接收能力相适应
技术的合理性:
技术的生命周期:投入期、成长期、成熟期和衰退期,所选技术应处于成长期
先进性:
技术上的先进和经济上的合理可行,应选择物料损耗小、循环量少,能量消耗少和回收利用好的生产方法 。
一个工业项目的产品可以从几种原料取,首先遇到的问题就是选择哪种原料。
(1)可靠性:
必须保证在其服务期限内有足够的、稳定的原料来源。
例如若是矿石原料,要看它的储藏量、品位和开采量。
凡以经过加工的原材料和部件作为原料的工业项目,最好与供应部门达成协议,以保证供应的可靠性。
(2)经济性:
在产品成本中,原料价格是一个重要因素。即要对各种原料投入后对单位成本的影响进行详细的分析。
原料价格受其供求关系变化的影响很大,要根据供求关系对将来的价格进行预测。
(3)合理性:
这主要是指对资源的综合利用是否合理。
例如煤、石油和天然气为主要起始原料的合理利用问题:在选择原料路线时,适当提高化工用煤的比例;油改煤,以节约石油消耗是合理的。
采用一定的原材料生产某种产品,可能有多种生产方法,每种生产方法所使用的生产设备、生产工具和工艺制造过程各不相同,也就是说,有不同的工艺技术路线。
每种工艺技术路线的投资费用和日常操作费用也不相同。把几种不同的工艺技术路线进行技术和经济比较,挑选出最适合的加以采用,就叫做工艺技术路线的选择,简称技术路线选择。
己内酰胺生产工艺
(二)确定各个过程或工序的组成
应采用多少和由哪些设备来完成这一生产过程,以及各种设备之间应如何连接,弄明确每台设备的作用和它的主要工艺参数。
例如:合成氨工艺中的变换工段
确定载能介质的技术规格和流向
常用的载能介质:水、水蒸汽、冷冻盐水、空气(真空或压缩)
(三)确定操作条件和控制方向
确定整个生产工序或每台设备的各个不同部位要达到和保持的操作条件。
>>>>1、反应器操作参数的确定
(1)温度
(3)压力
a、反应速度
b、反应物料的相态(如七项烃化和液相烃化)
c、后续分离要求(希望水冷后就产生气液两相)
(4)反应的转化率
a、准化率和所需反应时间的关系
b、各种转化率下的产品分布
c、反应系统和分离系统的设备价格
>>>>2、精馏塔工艺参数的确定
(1)塔压(实质上是塔顶塔釜温度选取的问题)
a、尽量避免真空操作(增加真空泵和塔径)
b、常压下能用普通冷却水冷却,就不宜采取加压
c、对于>1.6MPa时,究竟采用低压冷冻还是高压冷却,需要做方案比较。
(2)回流比
a、对于价格高昂的公用工程,取常规R/Rmin(1.11~1.24)的范围低限。
b、若回收的冷量或热量可利用,取常规R/Rmin的高限。
c、对于产品纯度极高的精密精馏,取较大R/Rmin值(因为取常规R/Rmin较小,塔板数会急剧增加)
(3)产品纯度和回收率
正确选择产品的纯度有重大的经济意义。
(四)确定控制方案
确保各生产工序和每台设备本身的操作条件,及实现各生产过程之间、各设备之间的正确联系,需要确定正确控制方案,选用合适的控制仪表。
d、塔压调节
(五)确定安全技术措施
设置相应的预防和应急措施,如阻火器、报警装置、爆破片、安全阀、安全水封、放空管、溢流管、泄水装置、防静电装置、防雷装置和事故贮槽等。
(六)原料与能量的合理利用;
计算并确定各个生产过程的效率,得出全装置的最佳总收率,同时合理地做好能量回收与综合利用,降低能耗以确定水、电、蒸汽和燃料的消耗
(七)制定“三废”处理方案;
对全流程中所排出的三废要尽量综合利用,对于暂时无法回收利用的,则须进行妥善处理
工艺流程设计和车间布置设计是决定整个车间(装置)基本面貌的关键性的步骤,对设备设计和管路设计等单项设计也起着决定性的作用。
流程设计的主要任务包括两个方面:
一是确定生产流程中全部生产过程的具体内容、顺序和组合方式,达到由原料制得所需产品的目的;
二是绘制工艺流程图,要求以图解的形式表示生产过程中,当原料经过各个单元操作过程制得产品时,物料和能量发生的变化及其流向,以及采用了哪些化工过程和设备,再进一步通过图解形式表示出化工管道流程和计量控制流程。
1、搜集资料,调查研究
要根据建设项目的产品方案及生产规模,有计划、有目的地搜集国内外同类型生产厂的有关资料,包括技术路线特点、工艺参数、原材料和公用工程单耗、产品质量、三废治理以及各种技术路线的发展情况与动向等技术经济资料。
掌握国内外化工技术经济的资料,仅靠设计人员自己搜集是不够的,还应取得技术信息部门的配合,有时还要向咨询部门提出咨询。
搜集设计资料的原则和步骤
(1)资料的完整性
全面的、完整的资料数据能够反映客观事物的全过程,才能用于设计。
(2)资料的正确性
正确的资料数据具有再现性,能反映客观事物的本质规律,才能用于设计。
(3)资料的适用性
科学技术都是有条件依据的,搜集资料要严格注意资料的适用条件。
(4)资料的恰当性
资料年代的差异会造成技术上的不同,在整理、分析资料时应注意资料恰当性,不可盲目一味追求先进性,要综合考虑整个设计的技术水平与建设项目的投资总额。
2、确定方案,落实设备
设备是完成生产过程的重要条件,是确定技术与工艺流程的时必然要涉及到的因素,因此要足够重视。
①确定生产线数目
大型装置与相同生产能力的数个小型装置相比优点:节约建设投资,占地少,自动化程度高等;缺点:附属设备贵,大都无备用设备,出故障只好停车;
若以单生产线的大型装置与生产能力相同的双生产线小型装置相比,开工率高时,则大型装置的经济效益好。假如开工率不足或生产负荷常变化,尤其是几种牌号的产品经常换产时,则双线小装置的经济效益好。
因此对于生产规模较大,涉及到是否实施大型化时需仔细分析比较。
②确定操作方式
尽量采用连续化操作方式。有时也采用间歇与连续联合操作化方式。有些过程采用间歇操作反而更有利些,如用蒸馏釜处理精馏塔塔釜的高沸点残液。
③确定主要生产过程
先抓住全流程的核心---反应过程,从它入手来逐步建立与之相应的生产过程。即原料→预处理过程→反应过程→产物后处理。
④确定辅助过程
降低能耗,提高能量利用率的过程。如反应热、位能、静压能等的利用。三废处理过程。为稳定生产而设立的过程(如缓冲、中间贮存)。
⑤合理确定操作条件
如高压反应过程,要求在原料贮罐到反应器间必须设立升压过程和相应的压缩机,而在反应器到产品间必须设立减压过程和相应的设备。
又如确定了反应器内的操作温度和允许波动范围,就要相应地设立供热或移热设施及手段(如夹套内泠管等),同时建立自动调剂温度的控制系统。
⑥考虑流程的弹性和进行设备设计
即全流程设计要考虑综合生产能力的弹性:应估计全年生产的不均衡性,各过程间所选设备的操作周期及其不均衡性,还要考虑因生产管理和外部条件等因素可能产生负荷的波动,这些均通过调研和参加生产实践来确定弹性的适宜幅度。
对设备的余度的考虑:原则上既不超过又不少于设计负荷,并且尽可能使各台设备的能力一致,以避免由于设备能力不平衡而造成浪费。
在考虑了全装置的弹性和各设备的余度以后,就可进行设备选型和设计计算了。
⑦确定控制系统
要根据各过程间是如何连接的、各过程又靠什么操作手段来实现的等等来确定它们的控制系统。
要考虑正常生产、开停车和检修所需的各个过程的连接方法,此外还要增补遗漏的管线、阀门、过滤密封系统,以及采样、放净、排空、连通设施,逐步完善控制系统。
注意:在这个过程中,与自控专业共同商定控制水平,进而设计全流程的控制系统和仪表系统,画在流程图上,完成PID。
⑧逐步完善和简化所设计的流程
要从各方面着手来逐步完善和简化:考虑到开停车和事故处理等问题,因而设置事故贮槽,增加备用设备以利于必要时可以切换使用。有时需设置自动往聚合设备内加终止剂的装置。
尽量简化对水汽泠冻系统的要求,尽可能采用单一系统。当装置本身需要用到几种不同压力的蒸汽时,应当尽可能简化或统一对蒸汽压力的要求。
尽量减少物料循环量,在切实可行的基础上采用新技术,提高单程转化率以及简化流程等等。
3、全面分析,对比比较
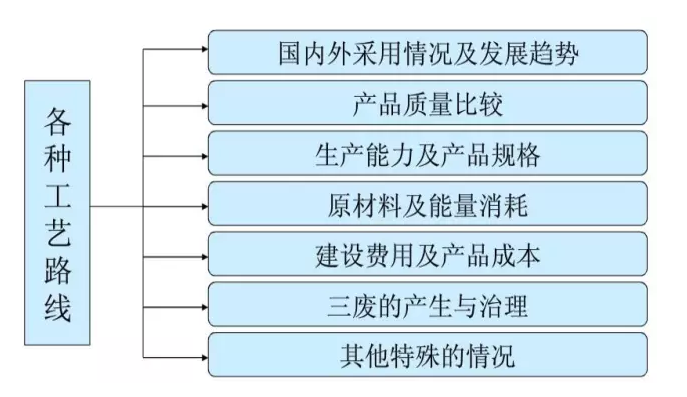
应当尽量从实际可能出发,多搞一些流程设计方案,然后进行全面的综合比较,从中找出最优的方案作为流程设计的成果。
工艺流程设计方法
首先要看所确定的生产方法是正在生产或曾经运行过的成熟工艺,还是待开发的新工艺。前者是可以参考借鉴但需要局部改进或局部采用新技术、新工艺的问题;后者须针对新技术开发进行概念设计。
(1)定反应器:
根据反应过程的特点、产品要求、物料特性、基本工艺条件来决定采用反应器类型及决定采用连续操作,还是间歇性操作。
有些产品不适合连续化操作,如同一生产装置生产多品种或多牌号产品时,用间歇操作,更为方便。
物料反应过程是否需外供能量或移出热量,都要在反应装置上增加相应的适当措施。
如果反应需要在催化剂存在下进行,就须考虑催化反应的方式和催化剂的选择。
一般说确定主反应过程的装置,往往都有文献、资料可供参考,或有中试结果。现有工业化装置可以借鉴、参考,因此并不复杂。
(2) 设计原料预处理过程
根据反应特点,必然对原料提出要求,如纯度、温度、压力以及加料方式等,以保证反应过程的实现。
原料预处理过程:固体:粉碎、溶解---目数、浓度、纯度液体:配制、混合---浓度、均一气体:配比、压缩---浓度、输送
原料预处理过程可以牵涉到:粉碎、筛分、配制、混合、压缩、提纯等单元操作。这些操作过程主要根据原料的性质及处理方法选择不同的装置进行组合。因此,设计的工艺流程就有所不同。
(3)设计产物的后处理过程
根据反应原料的特性和产品的质量要求,以及反应过程的特点,实际反应过程可能会出现下列情况:
①除了获得目的产物外,由于存在副反应,还生成了副产物。
②由于反应时间等条件的限制或受反应平衡的限制,以及为使反应尽可能完全而有过剩组分。
③原料中含有的杂质往往不是反应需要的,在原料的预处理中并未除净,因而在反应中将会带入产物中,或者杂质参与反应而生成无用且有害的物质。
④产物的集聚状态要求,也增加了后处理过程。某些反应过程是多相的,而最终产物是固态的。
因此用于产物的净化、分离的化工单元操作过程,往往是整个工艺过程中最复杂、最关键的部分。
产品分离包括:固液分离---过滤、离心液液分离---蒸发、精馏、萃取气液分离---吸收
产品分离牵涉到的单元过程:过滤、离心、蒸发、精馏、萃取、吸收等单元操作过程。这些单元操作过程,同样应根据被分离产物的特征,设计与之相适应的单元过程。
产品精制:对产物进一步纯化,以满足产品的质量要求。液体---精馏、浓缩、结晶固体---重结晶气体---吸收
产品精制牵涉到的单元过程:精馏、浓缩、结晶、重结晶等单元操作过程。这些单元操作过程,同样应根据产品的质量要求,设计与之相适应的单元过程。
(4)设计产品的后处理过程
经精制后的产物,成为最终的产品还需要干燥、包装、储运等过程。 固体---干燥、包装 液体---灌装气体---灌装
储运包装过程牵涉到的单元操作过程有:干燥、计量、包装等过程,应根据产品的特性进行设计工艺过程。
(5)设计未反应原料的循环或利用以及副产物的处理
由于反应不是全部,剩余组分在产物处理中被分离出来,一般应循环回到反应设备中继续参与反应。
(6)确定“三废”排出物的处理措施
在生产过程中,不得不排放的各种废气、废液和废渣,应尽量综合利用,变废为宝,加以回收。无法回收的应妥善处理。“三废”中如含有有害物质,在排放前应该达到排放标准。
因此在化工开发和工程设计中必须研究和设计治理方案和流程,要做到“三废”治理与环境保护工程、“三废”治理工艺与主产品工艺同时设计、同时施工,而且同时投产运行。按照国家有关规定,如果污染问题不解决,是不允许投产的。
(7) 确定公用工程的配套措施
在生产工艺流程中必须使用的工艺用水(包括作为原料的软水、冷却水、溶剂用水以及洗涤用水等)、蒸汽(原料用汽、加热用汽、动力用汽及其他用汽等)、压缩空气、氮气等以及冷冻、真空都是工艺中要考虑的配套设施。
至于生产用电、上下水、空调、采暖通气都是应与其他专业密切配合的。
(8) 确定操作条件和控制方案
一个完善的工艺设计除了工艺流程等以外,还应把投产后的操作条件确定下来,这也是设计要求。
这些条件包括整个流程中各个单元设备的物料流量(投料量)、组成、温度压力等,并且提出控制方案(与仪表控制专业密切配合)以确保能稳定地生产出合格产品来。
(9) 制定切实可靠的安全生产措施
在工艺设计中要考虑到开停车、长期运转和检修过程中可能存在各种不安全因素,根据生产过程中物料性质和生产特点,在工艺流程和装置中,除设备材质和结构的安全措施外,在流程中应在适宜部位上设置事故槽、安全阀、放空管、安全水封、防爆板、阻水栓等以保证安全生产。
(10) 保温、防腐的设计
这是在工艺流程设计中的最后一项工作,也是施工安装时最后一道工序。
流程中应根据介质的温度、特性和状态以及周围环境状况决定管道和设备是否需要保温和防腐。
工业生产中,一个过程往往可以有多种方法来实现,例如液固混合物的分离,可以用离心、沉降、压缩和真空过滤等方法;含湿固体的干燥,可以用气流、双锥、滚筒、箱式、沸腾等干燥方法,这些也都需要进行方案比较,因地制宜地选择一种最佳工程方案。
一个优秀的工程设计要在多种方案的比较中才能产生。进行方案比较首先要明确判据,工程上常用的判据有产物收率、原材料单耗、能量单耗、产品成本、工程投资等。此外,也要考虑环保、安全、占地面积等因素。
进行方案比较的基本前提是保持原始信息不变。过程操作参数如温度、压力、流速、流量等原始信息,设计者是不能变更的。设计者只能采用各种工程手段和方法,保证实现工艺规定的操作参数。
生产工艺流程设计牵涉面很广,其目的是把各个生产过程按一定的顺序和要求有机地组合起来,进而绘出生产工艺流程图来知道设备的安装和指导生产操作。生产工艺流程的设计需要经历生产工艺流程示意图、生产工艺流程草图、带控制点的生产流程图三个阶段。
来源:一点化工