内蒙古泰和煤焦化集团有限公司“4.8”爆炸事故
一、事故调查分析
(一)事故概要
1、事故简介
2014年4月8日上午10时45分左右,内蒙古乌海市泰和煤焦化集团有限公司化产车间脱硫工段脱硫液循环槽发生爆炸事故,造成3人死亡,2人受伤,直接经济损失约230万元。
2、事故原因
(1)直接原因
此次管道变更改造在未与生产系统隔绝、未进行吹扫、置换,动火点未隔离,未进行气体分析确认,违章用电焊明火作业,致使电焊火花通过未封死的人孔,引爆被脱硫液夹带并进入循环槽内的煤气。
(2)间接原因
①作业票证许可过程执行不严,作业票证管理不到位。此次脱硫工艺变更,涉及到动火作业。对易燃易爆、有毒有害气体的风险辨识不到位,违反《化学品生产单位动火作业安全规程》。
②变更管理制度执行不到位。此次工艺及管道变更改造前未对变更过程产生的风险进行分析和控制;未履行变更审批程序。
③工艺设备技术管理缺失,技术培训考核不到位。公司未设技术负责人,化产车间未配工艺和设备技术员;技术资料管理缺失。
(二)基本情况
1、事故有关单位情况
乌海市泰和煤焦化有限公司于2007年11月6日工商注册成立,位于乌海经济开发区海南工业园西来峰项目区。2011年5月20日,乌海市泰和煤焦化有限公司更名为乌海市泰和煤焦化集团有限公司,以乌海市泰和煤焦化有限公司为龙头,集采煤、洗选、煤焦、煤化工为一体的大型民营集团公司。现有职工900人。内设财务部、行政部、企管部、安环部、质计部、供销公司等六个部门。董事长兼总经理郭某,负责集团全面工作。副总经理张某负责安全生产工作,分管焦化厂和安环部。安环部部长王某,有9名工作人员,调度主任兼安全员罗某等4人负责焦化厂安全管理。该公司捣固焦项目总投资4.3亿元,2008年经自治区发改委批准立项,2009年6月建成,生产规模为96万吨/年捣固焦,副产品煤焦油4.3万吨/年,粗苯1.1万吨/年,硫磺0.135万吨/年。于2013年10月24日取得安全生产许可证,许可范围为焦炭、粗苯、焦油、硫磺、硫胺。焦炉煤气和煤焦油全部供乌海市黑猫炭黑有限公司炭黑项目。
焦化厂现有职工360人。厂长杨某负责生产和安全工作,总工程师陈某负责1#焦炉的技改工作(1#焦炉因地基下陷于2014年1月8日停产)。焦化厂由备煤车间、炼焦车间、化产车间和电仪车间组成,化产车间下设煤气冷凝鼓风工段、脱硫锅炉工段、硫胺粗苯工段和机修工段。化产车间主任任某负责全面工作,副主任张某协助车间主任负责生产、设备、安全管理及日常工作。脱硫锅炉工段工段长吕某负责脱硫工段和锅炉工段全面工作。
(三)事故发生时间序列
日期 | 时间 | 描述 |
2月28日 | 泰和煤焦化将脱硫工艺由碱法变更为氨法,发现清液排入泵房的低位槽后气味太大影响工人操作。 | |
3月20日 | 化产车间副主任张某(化产车间主任任某出差)安排吕某将清液管道由排入低位槽改为排入脱硫液循环槽内。 | |
3月26日 | 任某出差回来,认为管道改造错误,会导致清液温度影响脱硫液温度,造成脱硫液循环槽内的脱硫液副盐含量逐渐升高,从而影响脱硫效率和后续生产工艺。随即让张某和吕某重新对设置在脱硫液循环槽槽顶上的清液管道进行改造,但未按规定要求进行设计和编制技术改造方案。 | |
4月7日 | 09:00 | 操作脱硫工段长吕某与维修工段长魏某、维修班长魏某及维修工郑某、石某等人到脱硫液循环槽现场确定管道改造方法。 |
4月7日 | 09:30 | 吕某把阀门和法兰拿到维修班,让维修工拉管子备料。 |
4月7日 | 16:30 | 吕某去调度室开好动火安全作业证,在当事人不知情的情况下,顶替化验员延某填写虚假动火分析结果并签字;代替动火监护人脱硫班长毕某、动火监护人维修班长魏某、动火人维修工郑某签字,等待第二天有关领导和人员签字。 |
4月8日 | 08:50 | 吕某分别找车间副主任张某、车间主任任某、安环部安全员焦某和厂长杨某在动火安全作业证上签字,并把办理好的动火安全作业证交给维修工石某。 |
4月8日 | 09:00 | 维修班长魏某带领维修工郑某、石某、靳某接好电焊机地线,用绳子将做好的管件、焊把及焊线拉至循环槽顶。 |
4月8日 | 09:30 | 脱硫工段丙班班长毕某通知电工李某接电(临时用电作业证已办理),随后上到槽顶,并将灭火器和水桶吊到槽顶。 |
4月8日 | 09:40 | 魏某等人开始改管作业,先拆卸原通往循环槽顶部人孔清液进液管前端约400mm处的4孔法兰,发现清液管上法兰螺栓锈蚀无法拧开,于是石某用电焊呲断螺栓打开法兰(距人孔水平距离251mm,垂高距离346mm)。毕某发现焊渣煨燃了槽顶的保温棉,就对法兰下部的焊渣及周边洒水以防着火。 |
4月8日 | 09:50 | 法兰被拆开,取出插入人孔的清液管,石某将人孔用盖板盖住,但未完全盖严。随后石某用电焊在剩余的清液管上(距离法兰150mm)呲开孔并焊接立管,立管上自带弯头(指向事故槽B),又在通向事故槽B的管上用电焊呲开孔,焊接通向事故槽A的短管。 |
4月8日 | 10:30 | 焊缝焊接作业完成三分之二时,魏某说要安装阀门,毕某从循环槽下去取阀门,同时安排当班脱硫泵工王某上槽顶代替履行监护职责。毕某取回三个阀门后,王某用绳索将阀门提到槽顶,然后王某和靳某上好两个阀门。安装第三个阀门时,由于通往循环槽人孔的管道上原法兰与阀门的法兰螺丝孔对不上,石某用电焊呲原法兰螺丝孔。 |
4月8日 | 10:45 | 脱硫液循环槽槽顶开始抖动,发出轰隆轰隆的声响,靳某意识到循环槽可能爆炸,立即翻越护栏,准备从槽顶往下跳,刚迈出一条腿,瞬间循环槽发生爆炸。 郑某、魏某、王某3人被爆炸冲击到脱硫液循环泵房房顶,事故造成郑某、魏某、王某、石某死亡,靳某受伤。 |
(四)事故损失情况
事故造成3人死亡,1人重伤,1人轻伤,直接经济损失约230万元。
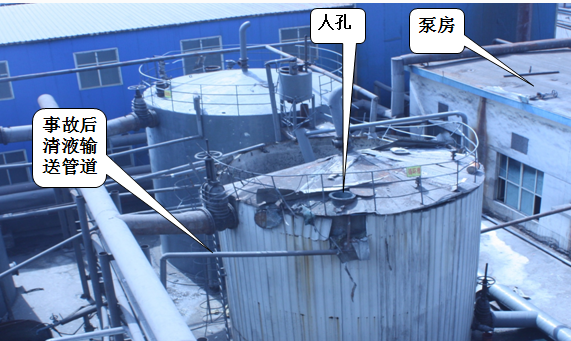
(五)事故原因分析
1、直接原因分析
此次管道变更改造是在生产系统运行状态下,违反《化学品生产单位动火作业安全规程》和公司《动火安全管理制度》的规定,在未与生产系统隔绝、未进行吹扫、置换,动火点未隔离,未进行气体分析确认,违章用电焊明火作业,致使电焊火花通过未封死的人孔,引爆被脱硫液夹带并进入循环槽内的煤气。
2、间接原因分析
(1)作业票证许可过程执行不严,作业票证管理不到位。
①此次脱硫工艺变更,涉及到动火作业。对易燃易爆、有毒有害气体的风险辨识不到位,违反《化学品生产单位动火作业安全规程》,将017号动火作业由特殊动火降为二级动火,降低动火等级;办证人提前一天办理017号动火安全作业许可证,并代替动火人、动火监护人签字,虚填有害气体化验分析结果,未制定落实安全措施方案;车间、焦化厂、安环部负责人在未确认和核实安全措施方案的情况下盲目签字审批。
②企业虽然按照《化学品生产单位危险作业安全规范》标准制定了《八大作业票制度》,但未认真组织对办证人、管理人员进行系统培训考核。造成办票过程中随意填写、代替签字,层层把关流于形式。
③安全作业许可证的管理失控,在调度室随意放置,无专人管理,对签字人员不进行核实,不到现场核实安全措施,安全员、有关领导就签字。
(2)变更管理制度执行不到位。此次工艺及管道变更改造未严格执行该公司《变更管理制度》,实施变更前未对变更过程产生的风险进行分析和控制;未履行变更审批程序。
(3)工艺设备技术管理缺失,技术培训考核不到位。
①公司未设技术负责人,化产车间未配工艺和设备技术员。技术资料管理缺失,脱硫循环槽上封头与槽体采用点焊、多次工艺设备改造变更都未上图;脱硫工艺、设备、管道等四次改造变更,均未经专业技术人员设计或专业技术人员论证;脱硫工段随意改变工艺设备和管道,将脱硫工艺由碱法改为氨法,再改为碱法,又改为氨法,变更后不能满足工艺要求,重新改造变更管道,酿成事故。
②由于受市场因素影响,管理人员和作业人员流动频繁,对新录用的岗位工、机修工、电工,只是履行了三级安全教育,未开展针对性的风险控制、操作技能、工艺规程、检维修规程的培训考核,也未对新调岗和新上岗的工段、车间、分厂领导进行安全生产培训考核。员工安全意识淡薄,不具备相应的能力。
(4)隐患排查不彻底,未做到全覆盖。未严格按照《危险化学品企业事故隐患排查治理实施导则》定期进行全覆盖的隐患排查,焦化厂、车间、工段、班组、岗位的隐患排查都未排查出脱硫液夹带煤气造成循环槽内易燃易爆混合气体富集的危害、未化验过气体组分、电焊线与槽体搭接、循环液槽顶封头与槽体点焊等隐患,也未排查许可作业证管理缺陷和电工无证上岗等隐患。
(5)企业风险管理不到位。焦化厂、车间、工段、班组、岗位风险辨识缺失,对脱硫循环槽内富集氢气、一氧化碳等易燃易爆气体没有分析评估到,对脱硫液夹带煤气造成循环槽内易燃易爆混合气体富集的危害也未辨识到,也未制定管理、工程、技术、应急等措施。安全生产管理机构与生产管理合并交叉,不能正确行使安全生产管理职责。
二、事故应急处置
事故发生后,当班操作工梁某立刻拨打120急救电话,集团董事长兼总经理郭某等公司领导听到爆炸声响后立即到达现场,启动了公司事故应急预案,对现场进行了断电、关闭蒸汽和循环泵,并组织人员进行抢救,同时向有关部门报告事故情况。11点05分救护车赶到,将5人送往海南区人民医院。郑某、石某、魏某经医院确认死亡。王某、靳某后被转送石嘴山第一人民医院救治,其中王某伤势较重,自主呼吸困难,5月12日抢救无效死亡;靳某伤势较轻,经过3次手术后,意识逐渐恢复清醒。
三、反思与建议
(一)反思
事故暴露出企业在作业安全管理、变更管理和风险管理方面存在问题,危险作业许可制度、变更管理制度执行不到位,形同虚设,风险辨识能力不足。许可票证等级无人把关,危害识别不全面,审批环节管理失控;作业过程出现无人监管情况;进行工艺变更前,不履行变更审批程序,不对变更过程产生的风险进行分析和控制;企业没有意识到循环槽内存在爆炸性混合气体,动火作业具有燃爆的危险。
(二)建议
1、加强作业安全管理。严格许可票证管理,把票证管理上升到企业一级管理范畴,要对焦化厂的所有车间、工段、班组、岗位重新组织全覆盖的风险评估,重新确定风险等级。对办票人员、管理人员、审批人员、检维修人员、监护人员组织开展培训考核,督促其认真熟练掌握如何办票证、如何划分作业证等级、如何制定落实安全措施、安全方案、如何审查审批不同等级的许可票证。坚决杜绝冒名顶替、虚填分析结果,以及审批人不到现场确认就签字审批等现象。
2、加强变更管理。严格执行《国家安全监管总局关于加强化工过程安全管理的指导意见》,在工艺、设备、仪表、电气、公用工程、备件、材料、化学品、生产组织方式和人员等方面发生的所有变化,都要纳入变更管理;严格变更管理审批程序。
3、加强安全教育培训。要牢固树立“安全培训不到位是重大安全隐患”的理念。强化对工艺、检维修、应急处置、风险辨识及管控方面的安全知识培训考核,建立“全员、全过程、全方位”的“三全”安全培训考核制度;强化特种作业管理,严格特种作业人员持证上岗制度;认真落实主要负责人强制安全培训考核制度,确保管理人员安全生产能力满足生产要求持证上岗;聘请煤焦化专家,对化产车间进行操作技术培训考核,切实提高员工的安全生产技术和风险辨识、应急处置能力。
4、进一步加大对“三违”现象的查处力度。从制度上、规程上、作业上进一步规范整治“三违”现象,要将各班组、各工段、各车间、各分厂常见的或易发生的“三违”现象造册,教育警示张贴到岗位,强化日常的培训考核,让每一位员工熟记于心,牢记于脑,切实筑牢安全生产防线。
5、加强风险管理,确保风险可控可防。采取公司包分厂、分厂包车间、车间包班组、班组包岗位的办法,发动全体员工参与深入开展岗位风险辨识,对辨识出的岗位风险要采取管事顶用的管理、工程技术、应急处置三大措施,确保岗位风险时时刻刻在可控范围内。