变更管理基本概念
“变更管理”最早于20世纪60年代应用于核电行业,后来被西方的国防工业采纳,大约在1976年开始在化工行业应用。1992年,OSHA在其颁布的PSM中将“变更管理”作为其中一要素,以法规的形式要求企业加强对变更的管理。OSHA规定,对过程系统进行变更时,应全面评估变更对于员工安全、健康和环境的影响,并需要明确对操作规程所进行的修改。
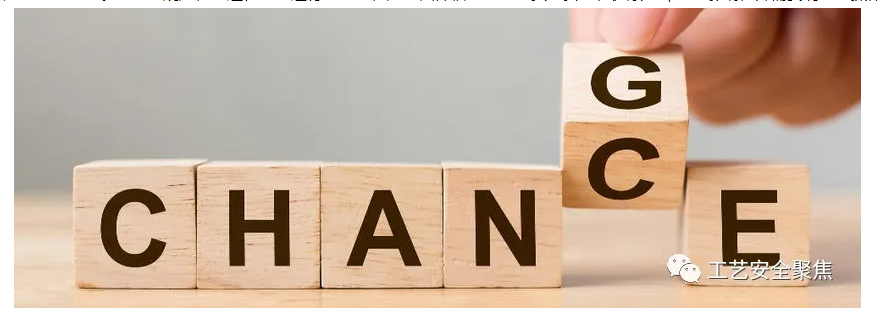
首先,“同类替换”不属于变更。所谓同类替换是指用相同规格的设备、仪表或管道替换现有的设备、仪表或管道,而且不必因为这项改变而修改书面的设计规格文件。例如,用相同规格的垫片替换旧的垫片,用相同规格的设备或阀门替换现有设备或阀门,都属于同类替换。有些公司的要求更严格,对于设备替换,不但要求相同规格,而且要求出自同一厂家,才是同类替换。同类替换不属于变更的范围,不必遵循变更管理程序,但仍然需要遵守相关的维修程序和其他作业程序。其次,在设计范围内进行的日常操作和维护作业也不属于变更的范畴,不受变更管理程序的约束,但可能需要遵守其他安全作业规定,如动火作业许可、受限空间进入许可证等。例如:
设备和管道的日常检查;
换热器或其他设备的清洗;
仪表的维修和校验;
在设计条件允许的范围内调整工艺参数;
在设计条件允许的范围内调整产能。
不是所有的改变都会影响系统的安全性,只有可能带来危害、影响过程安全的,如,针对化学品、技术、设备、设施和操作程序的改变(同类替换除外),称为变更。石化、化工领域涉及过程安全的变更通常包含以下四类:
过程技术变更:
主要是涉及过程流程的改变,如原料化学品的改变、过程操作条件的改变以及操作程序的改变。
作业程序变更:
主要是操作人员或维修人员更改操作程序、维修程序或其他安全作业指导书。
工厂设施变更:主要是对工厂现场物理条件的改变,包括暂时或永久性替换设备/设施(同型替换除外)。
组织机构变更:主要是工厂生产、维修和安全等相关人员和职位的改变,包括人员更替、职位增减等。如减少每个班组的操作人员、更换员工职位和减少(或增加)工作职位等。这些改变可能使从事某项工作的操作人员减少,或某职位的操作人员缺乏所需的经验和技能,从而影响过程安全。改变组织机构时,要关注是否有足够且能胜任的人,承担起有关安全工作任务,以及分工和责任是否明确、合理等。
案例解析
结合下述案例,对变更管理与过程安全管理之间的联系,进行探讨。1974年6月,英国Flixborough Nypro化工有限公司,己内酰胺装置,25A工艺单元反应器发生严重的爆炸事故,致使整座工厂几乎夷为平地。28人当场死亡,36人严重受伤,1821间房屋和167家商铺受损。事故发生前2个月,环己胺蒸汽从5号反应器泄漏,为了吸收环己胺蒸汽,装置使用临近的冷却水浇到5号反应器上,用来冷却和缓和泄漏的环己胺。浇冷却水,这个过程上的变更,在当时并未引起足够的重视。冷却水中的硝酸盐加剧了低碳钢反应器的腐蚀,反应器不得不被迫拆除,用20英寸临时管线进行代替。这次设备的变更,最终导致事故的发生。
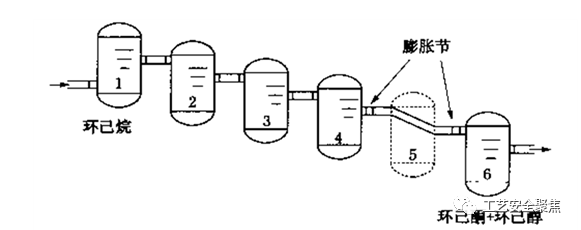
事故报告阐述:“引起灾难的原因是由于设施的改造打破了装置的完整性。”事发前操作人员用粉笔在维修地面上画了一个全尺寸的临时管线草图,却并未对管线连接进行应力分析和计算。变更管理的记录,应当有一个系统的文件进行备份。在对装置进行变更前,应对变更可能造成的后果进行全面的评估。变更管理的审查系统,应当由有能力的人员进行。
装置人员将冷却水浇在泄漏的反应器上,对反应器进行降温,这对反应器的正常操作来说就是一个过程变更,属于连续过程条件下的异常操作,需要首先进行危害识别及影响评估。
该事故的另一个重大过程变更是将5号反应器切除,用一段20英寸的管线代替,该项变更并不属于同类替换,而应该是设备变更。
在开展该项设备变更前,应该先精确的计算变更管线对过程参数的影响,然后根据计算结果进行过程安全分析,合理有效地分析该项变更可能引发的后果,只有识别出充分的保护措施,将后果降低至风险可接受范围之内,才可以开始实施该项变更的后续步骤。
装置的生命周期中,每时每刻都会发生变更,每一项变更都有可能会引发重大的安全事件或事故,只有对变更可能引发的风险进行深入的分析,才有可能从根源上减少事故发生的可能性。因此对变更的管理需要引起额外的重视,对于变更的处理更需要额外的小心。
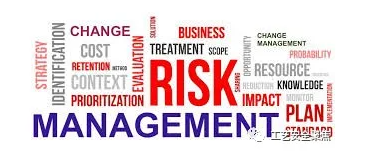
目前企业几乎都建立了变更管理制度,但是变更管理制度的合理性和相应管理措施的有效性如何,则不可一概而论。无论如何,企业应该关注的是,变更管理是非常系统化的管理,是企业风险管理的重要一环,不仅要正确的识别和认知变更,更重要的是,对于变更所产生的风险,能够正确的评估并进行合理控制,以预防事故的发生。