过程安全事故往往都是重大事故,对企业来说,此类事故一旦发生将很可能面临灭顶之灾。一个企业要保持可持续发展,必须要重视过程安全。长期以来,陶氏化学(Dow)非常重视过程安全事故(PSIs)的预防。基于安全生产对企业的重大影响,陶氏化学在总结多年生产实践和事故分析的基础上,逐步建立了自己的过程安全管理体系。早在1995年,陶氏化学及环保、健康和安全(EH&S)部门的管理层对外公布了未来10年的安全规划目标:大幅度降低事故的发生率。该目标的设定为推动安全绩效的突破性改进提供了契机,从图1可以看出过去10年,陶氏化学的PSIs减少了三倍以上(图1)。2005年,陶氏化学制定了另一个十年目标:将过程安全事故(PSIs)的数量和严重程度分别降低75%和90%。如图1所示,陶氏化学在2011年实现了这一目标并一直保持到2015年。
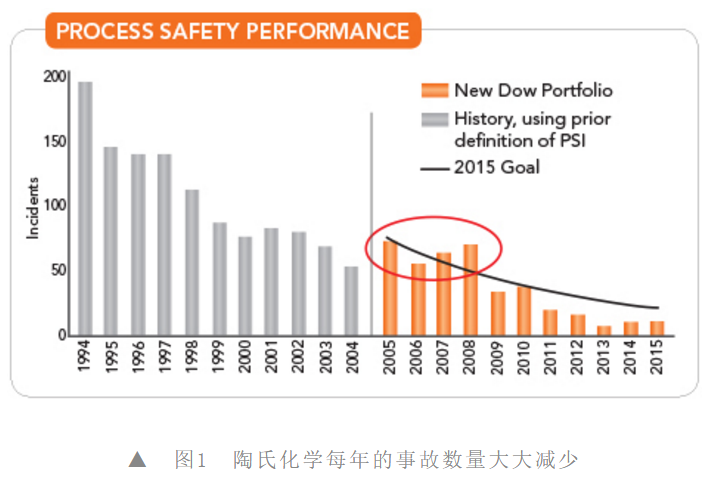
文章将分成两期和大家分享陶氏化学在减少过程安全事故方面行之有效的良好实践;本期将重点介绍一些关键措施,这些措施的实施使陶氏化学打破2005-2008年的瓶颈,实现事故率持续降低,争取达到安全零事故。
The Basis for Success 成功的基础
图2为我们展示的是构成一个行之有效的过程安全计划(Process Safety Programs)的三个基本要素。
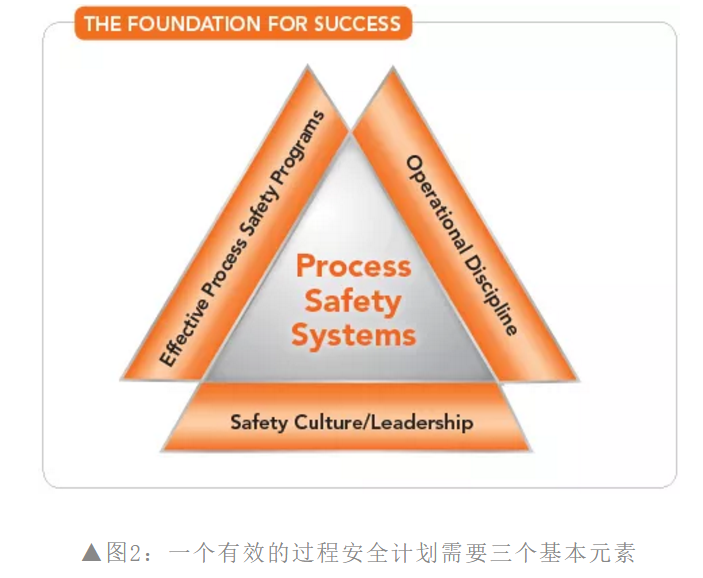
▲三角形的底部(基础)代表的是安全文化\领导力,企业各层级领导的支持是保障过程安全成功的重要基础。▲三角形的左边是陶氏化学在全球范围内实施的操作规程管理体系。这些体系包括过程风险管理标准(PRMS)、全球机械完整性安全标准(GMISS)以及人身安全标准(PSA)等。这些内部标准通常高于法定标准的最低要求。▲三角形的右边是操作规程(Operational Discipline)。过程安全体系的成功执行取决于操作规程的有效实施。如:为有效检查和减少由于机械完整性故障造成的Containment losses(设备泄漏),必须遵守机械完整性安全标准(GMISS)中的设施管路检查规程。PS:大家如果对Containment losses有更合适的翻译,欢迎留言探讨。Leadership at all levels 各级领导
陶氏化学致力于不断提高个人和过程安全绩效以符合公司的核心价值观,把EHS工作视为重中之重,并鼓励各个所属企业和职能部门的所有员工参与其中。陶氏化学明确要求所有员工都必须对安全负责,考核所属企业和员工的安全绩效以实现公司的安全期望值(safety expectations)。
领导力承诺至关重要。按照陶氏化学的过程安全愿景,企业管理人员的领导力对企业运营的实际成效影响很大。领导层制定安全指标和战略目标,投入必要的资源来推动、改进和维持过程安全绩效。举几个领导层直接参与的例子:1. 领导和管理(Leadership Governance):确保持续的安全支持性措施、资源和重点项目对于过程安全改进至关重要。企业EHS总监负责带领运营管理团队operation governance team(OGT)推动运营设施的EHS业务及岗位责任制。根据陶氏的EHS政策、标准和要求,实施岗位监督。OGT负责监察各设施的整体风险管理,从而改善EHS管理,并确保各所属经营企业及区域团队的管理按照陶氏化学的企业风险标准(Corporate Risk Criteria)。
2. 资金投入(Financial commitment):企业投入整体安全风险管控专项资金,确保及时完成过程安全项目,并通过风险评估确定这些项目的优先次序。企业、过程安全和EH&S的领导层共同负责这些过程安全建设项目,把企业风险管控专项资金作为EH&S优先资金,用于改善风险等级较高的整改项目。
3.工厂设施领导力(Facility leadership):每个工厂的生产负责人应充分了解该工厂设施的化学、技术和工艺安全风险。陶氏化学通过RC-PHA(反应性化学品-过程危险性分析)工作流程机制来衡量新生产负责人是否胜任该工作:即新上任的生产负责人需在90日内向领域专家、过程安全和EHS专家组成的专家组就RC-PHA做专项汇报。在此项工作流程完成之前,他无权批准高风险的变更管理审核。
注:RC-PHA(反应性化学品-过程危险性分析)是由一个多学科小组进行的为期1-2天的审查活动,内容包括:工艺化学、风险管理计划的完整性、最差情况的假设与主要防线的设立、历史事故、工艺变更、培训和教育计划、调查问卷、先期审查中所提建议的落实情况等。4.员工参与管理(Employee engagement):在日常生产操作中员工永远把EHS作为他们的首要任务。所有工厂设施员工包括操作人员都制定相应的个人健康与安全目标。企业领导对所有作业范围内的安全生产工作进行全过程的监督管理和指导。所有员工,无论职位高低,都有权上报安全生产问题,并采取措施保护自己以及作业场所的安全。假如操作员工发现安全问题,哪怕只是一处轻微泄漏,都有权关停装置。
过程安全计划的好坏取决于它的落实情况。陶氏化学不仅通过设定指标来实现各种安全目标,而且还采取必要的行动来达到和超过这个目标。因此,日常生产工作中遵守安全操作规程至关重要。本篇,我们将重点介绍促进陶氏化学在过程安全方面获得持续成功的其中两个操作规程体系,另外三个将在下期做详细介绍。为了预防发生频率低但后果严重的大规模事故,在进行风险评估时,需要基于最坏场景假设,并确保针对这类场景设计的保护层不受损害。陶氏化学设置了一些基本规则(Cardinal Rules)来确保对这些场景的高度认识,防止重大事故的发生。在过去的几年里,陶氏公司对每一项技术都制定了基本规则,然后将其传达到各个生产作业场所。这些原则遵循圣经十诫的形式,采用简短的语句,用“决不”(never)或“总是”(always)这样的绝对术语表示。基本原则最多控制在10-15条,强调重点。所有基本规则都是基于该项技术在相关行业内外发生的历史事故而制定的。所有涉及该项技术的人员都必须知晓、理解并遵守与之相应的基本规则。违反基本规则可能导致(在许多情况下已经导致)重大事故,对人员、财产和社区造成潜在影响。未造成事故的违规行为将被记录为未遂事故,并开展调查,将调查中获得的教训应用到技术当中,防止此类事件再次发生。 举个例子,2010年,陶氏化学丙烯酸单体技术负责人参照企业内外部的存储和装卸标准,制定了一份基本规则。这些标准包括大量关于安全装卸丙烯酸单体的详细规程和指南。其中很多规程和指南体现了良好实践并总结了从历史事件中吸取的教训。采用广泛的标准和制定一份基本规则表的优点是:可以将重要的概念提炼成简短的语句,并影响员工的工作方式。
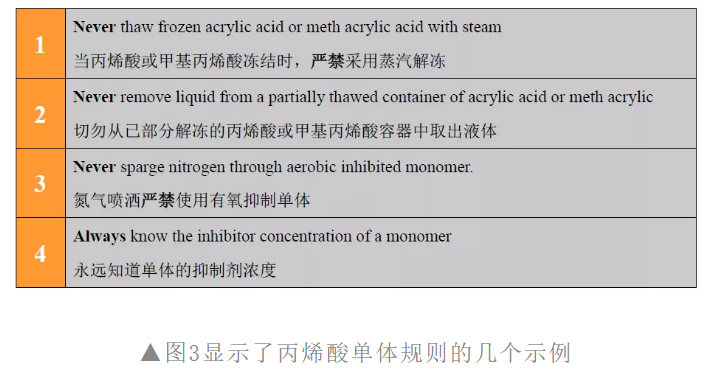
每个简短的语句都有详细说明来强调规则的重要性。这些详细说明包括对违反规则时可能发生(或已经发生)的情况、工厂中存在的危险以及应采取的最低保障措施。表1提供了图3中的一个规则的示例。
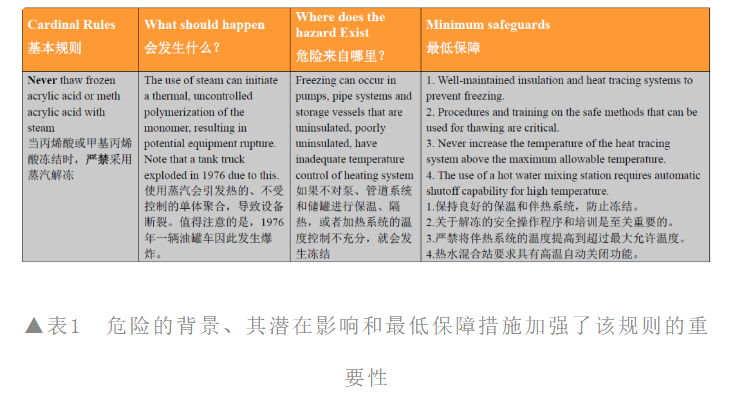
基本规则一经发布就将其纳入到所有与该技术相关的人员培训计划中。在技术专家的指导下,操作员、工程师、生产负责人和其他人员接受这些规则的培训并定期复训。此外,将这些规则应用到每个人的日常工作实践中。例如,在每个运行装置的控制室以及员工办公大楼的显著位置都会摆放一份基本规则副本供员工查看。

在陶氏化学以及整个行业经常发生以下各类事故:失控的化学反应、火灾和爆炸、压力容器超压、建筑物爆炸等等。这些事故都可能导致灾难性的后果:人员受伤或死亡、财产损失、建筑物破坏、业务中断、环境污染等。深刻吸取事故教训,防止悲剧重演至关重要。但是随着事故发生率越来越低,很多人也会因此放松警惕。大多数员工在职业生涯中可能从未亲身经历过重大事故,而事实上,这才是我们真正的目标:永远不要经历一次事故。将历史事故案例学习纳入到安全培训体系中,加强安全教育,可大大减少事故的发生。陶氏化学的培训内容包括:
培训计划中详细说明了工厂正在使用的化学物质的特性。包括一份完整的危化品清单;如何识别危化品;如何应对化学品接触;危化品的易燃性、毒性、反应性危害;以及在危险条件下(如高温和高压)操作的化学品的特性等。
这类培训包括反应性化学和与操作系统相关的危险,如工艺区域工作人员因系统操作失误导致威胁生命的事件发生。培训内容包括所涉及的化学物质、典型的初始事件以及事故影响的程度(距离/后果)等。培训中,将正常操作和异常情况的场景进行展示对比。
培训中介绍了可以提高安全系数的主要保护系统及其设计特征(例如,生产工艺中不需要加水、工艺布局和建筑设计等)。其中一个重点需要关注的是:有哪些防护措施是可以直接保护操作人员的,如应急响应程序。
培训中对重大历史事故进行回顾,包括最严重的易燃和有毒物质泄漏事故,以及设施或技术操作中发生的死亡事故。深入研究历史事故重点强调了危险的真实性以及保护装置的重要性。结合图文或视频更全面更清楚地帮助员工了解事件的后果。每个工厂设施必须开展培训。新员工必须接受入司培训,其他员工必须定复训,采用多种授课方式如面授或自主线上学习。下期将和大家继续分享其它3个重要措施,包括过程安全焦点(PSFP)、记录未遂事故(Near-misses)、根本原因调查(RCI)及经验分享。